From Iowa design lab to 3M accolades
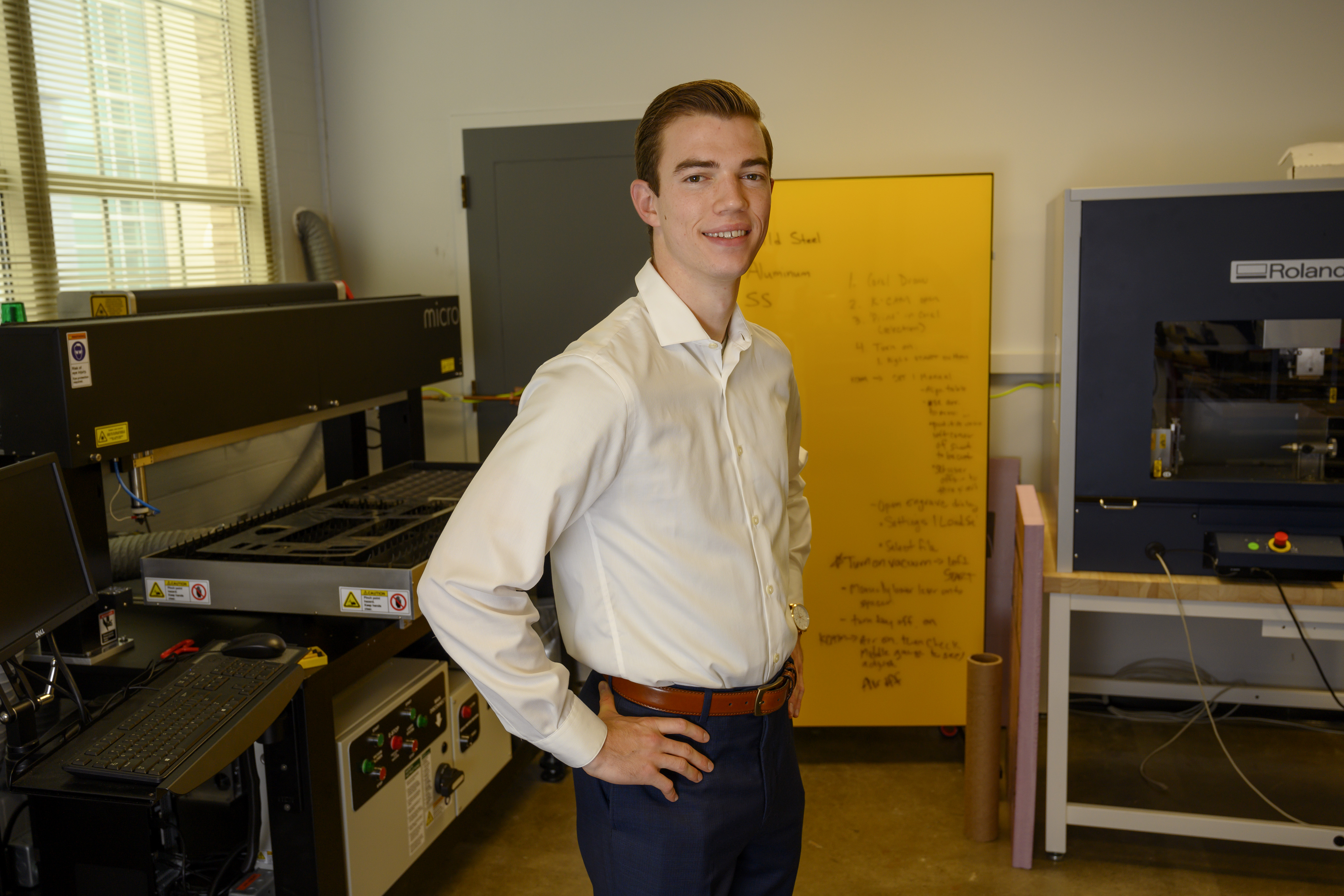
Zachary Ingram didn’t have to wait long to get a substantive assignment during his summer internship.
In his first week at the global manufacturer 3M, company scientists asked Ingram, who had just completed his junior year at the University of Iowa, to take a look at a better way to secure a catheter and figure out whether the redesign was commercially viable.
“I did an iterative process of coming up with ideas to test the device, getting data, and making incremental changes to try and squeeze as much positive performance out of it as we could,” says Ingram, a biomedical engineering major from Sioux City, Iowa.
Ingram’s work paid off handsomely: By the end of his 12-week internship, he had successfully tested a catheter-securement design and had improved the product so much that 3M plans to list him as the inventor if it files for a provisional patent.
“The amazing part was Zach designed the actual structure, the modifications, the testing,” says Audrey Sherman, a research scientist at 3M and Ingram’s supervisor. “He’s testing and then he realizes, ‘Well, if I did this, it will be better.’ He made enough of an improvement that we called it a discovery. He discovered another structure that was even better.”
Ingram credits his academic and lab experiences at Iowa for giving him the skills—and confidence—to tackle the challenge at 3M.
“That (experiential learning) really came in handy for what I was doing at 3M, because with the design work, I was doing modeling, 3-D cutting, and laser printing, and I had already learned those skills from some of my classes,” Ingram says. “Definitely, those application-type classes have been really helpful.”
In particular, Ingram mentioned classes taught by Colleen Bringman and Osama Saba, lecturers in the UI College of Engineering, who focus on biomedical device design and product development.
“I think the biggest hurdle with engineering students around Zach’s age is they have all this theory. They’re really good at solving equations or really good at math, and then all of a sudden they get asked to make something. Sometimes that can be really daunting. This class made them do it really fast and made them iterate on things and get comfortable with prototyping.”
One of the first classes Ingram took in the biomedical engineering track was Engineering Drawing, Design, and Solid Modeling, a course taught by Bringman. In that class, students learn how to conceptualize product design and investigate a product’s performance through computer simulations.
In spring 2019, Ingram advanced his knowledge in another Bringman class, Medical Device Design: The Fundamentals. In four weeks, Ingram’s team designed, created, and tested a prototype for a device that allowed a patient with an immobilized thumb to regain some function of the hand, such as being able to grasp a zipper and zip up a coat. The students used a 3-D printer to manufacture their creation.
“I think the biggest hurdle with engineering students around Zach’s age is they have all this theory,” says Bringman, who earned her bachelor’s, master’s, and doctoral degrees from Iowa and teaches full time in the Roy J. Carver Department of Biomedical Engineering. “They’re really good at solving equations or really good at math, and then all of a sudden they get asked to make something. Sometimes that can be really daunting.”
“This class made them do it really fast and made them iterate on things and get comfortable with prototyping,” Bringman continues. “You don’t have time to think about what won’t work because you have to make something.”
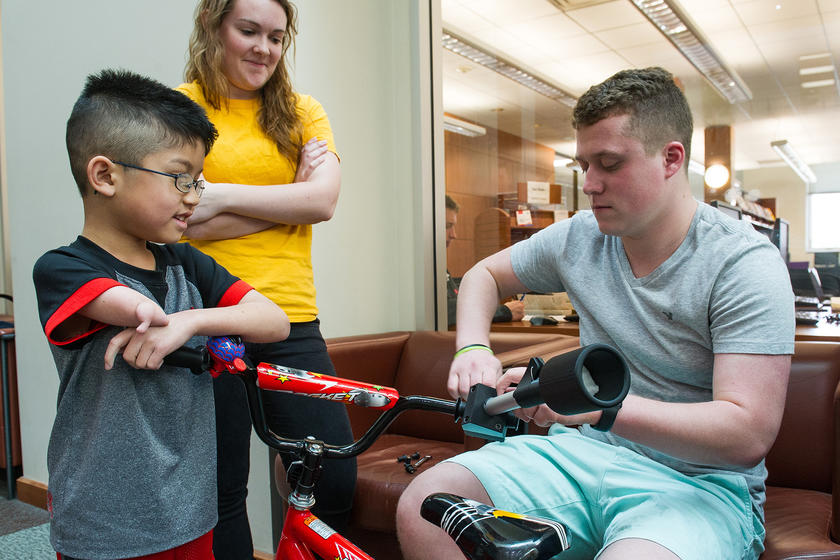
Biomedical engineering links biology, medicine, and engineering to improve human health. Many engineering students choose this major as preparation for medical school. The Roy J. Carver Department of Biomedical Engineering at the University of Iowa offers students great flexibility in career preparation. With the proper selection of elective courses, the curriculum affords numerous engineering specialties, or the opportunity to pursue advanced degrees in medicine, dentistry, pharmacy, physical therapy, or law.
“I found, personally, the most effective way for me to learn is to actually do things,” Ingram says. “And what Bringman’s classes did is they’d be short lectures going over what we’d be doing for the day, and then we’d go out and do it.”
In Saba’s class, Systems Instrumentation and Data Acquisition, Ingram learned how to incorporate electronics into product design. Students, working in small teams, must design and build a biomedical device that helps someone with a physiological need.
Saba gives the students wide latitude for their creation: Previous product incarnations have been prosthetics, heart monitors, temperature controls for an infant incubator, and devices that convert audio signals to light for the hearing impaired.
Ingram and his team created a sensor that picks up the signal from a contracting human muscle and transmits that signal to activate a prosthetic hand. The device may seem simple, but its execution involved a cascade of steps, such as sensing the electrical signal from the muscle, amplifying and filtering the signal, then converting the signal to a digital form that can be read and acted upon by a computer, which sends the instructions to the prosthetic hand.
“I tell them up front: It’s going to be tough, but in the end, you’ll learn a lot,” says Saba, who earned his doctorate in biomedical engineering from Iowa and who worked at the German manufacturing giant Siemens. “I’ve had a lot of my students who have gone out into the job market, and they come back to me and they say, ‘You know that I’m using this, this, and this on the job that I didn’t know anything about until I took this class.’ And, I say, ‘Well, I introduced it to you to give you a leg up, and the success you’ve had since is yours.’”
“The class was super hands-on,” Ingram says. “During the lab time, we were able to build these different devices and see how they actually worked, and not just hear about it. I think anytime I’m able to do that, it just sticks with me a whole lot more.”
At 3M, Ingram was placed in the company’s Medical Solutions Division and assigned to Sherman. After giving him a day to acclimate, Sherman set him up to begin testing the catheter-securement device.
Within a week, Sherman was gone, taking a vacation in France. Meanwhile, Ingram got busy testing the catheter device and seeking ways to make it more secure so it would lessen infection rates.
It wasn’t long before he was reporting progress to his boss.
“It was speedy. It was way beyond expectations,” Sherman recalls. “You say, ‘Yep, we want to prove that this is actually better, and by the way, go for it.’ That’s all on Zach.”
3M is determining whether the catheter-securement improvements merit a patent application. Sherman thinks it will.
As for Ingram, his experience at 3M, coupled with his classes, have solidified his plans after he graduates in May.
“I think it showed me how my career progression will go,” Ingram says. “I hope to get into a manufacturing role in a company and then, long-term, to get back into the research and product development role and making products.”